By Nirmal John
Unlocking the Future of Manufacturing: The Complete Guide to Smart Factories
Wednesday May 7, 2025
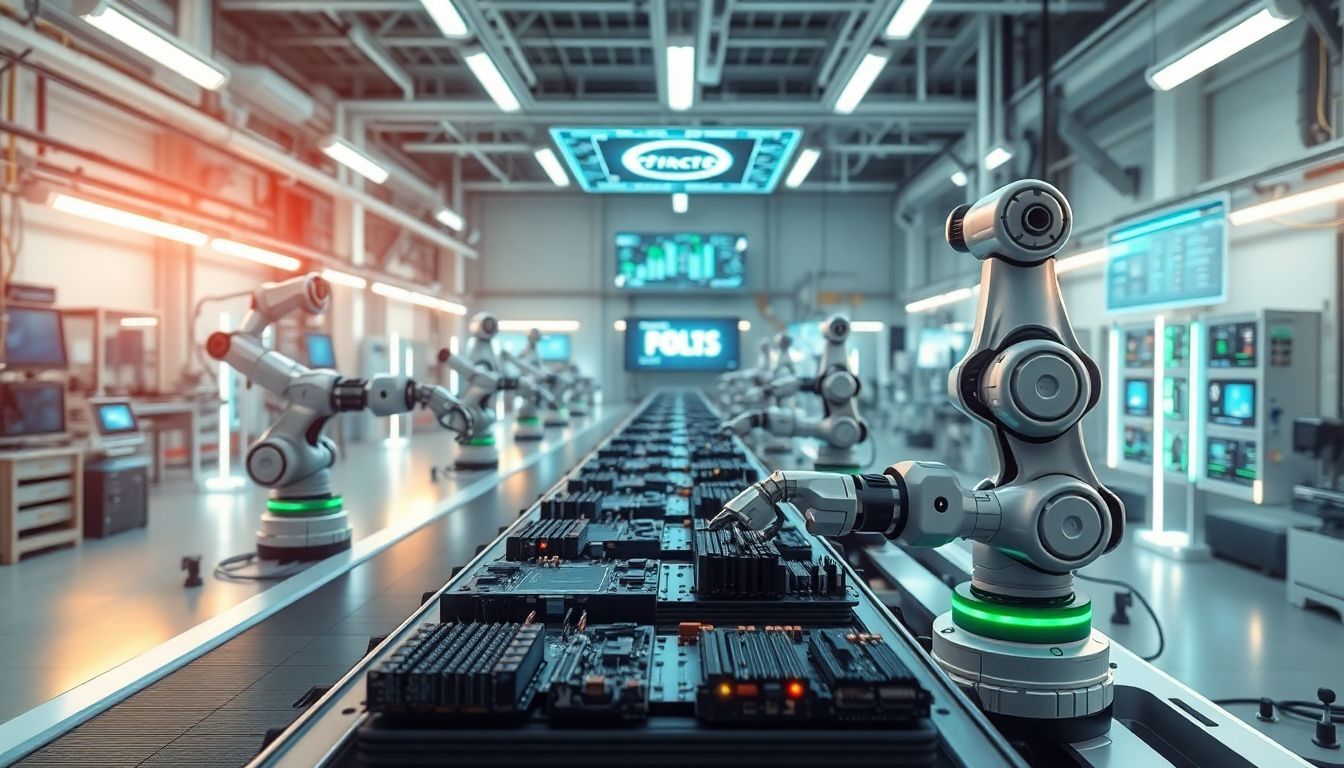
Unlocking the Future of Manufacturing: The Complete Guide to Smart Factories
Introduction: The Evolution of Smart Factory Technology
Manufacturing has undergone remarkable transformations throughout history. From artisanal craftsmanship to mechanized assembly lines, the industry has continuously evolved to meet changing demands. Today, we stand at the threshold of another revolutionary shift with the emergence of smart factory technology. These digitally-enhanced manufacturing facilities represent the next frontier in production efficiency and quality control.
A smart factory integrates advanced digital technologies to create a more connected, optimized, and efficient manufacturing process. Companies worldwide increasingly recognize the competitive advantage these facilities offer, with global investment in smart factory solutions reaching unprecedented levels. According to recent industry reports, the global smart manufacturing market is projected to grow from $156 billion in 2023 to over $384 billion by 2029, representing a compound annual growth rate of 16.3%.
This comprehensive guide explores how smart factories are reshaping manufacturing landscapes through enhanced connectivity, real-time analytics, and autonomous systems. We’ll examine the foundational technologies, implementation strategies, tangible benefits, and future directions of this transformative approach to production.
What Is a Smart Factory? Defining Key Concepts and Technologies
The Smart Factory Within Industry 4.0
A smart factory represents a manufacturing facility primarily operated through digital systems and advanced automation technologies. It stands as a cornerstone of Industry 4.0, characterized by comprehensive connectivity and real-time data exchange across all production elements. Unlike traditional manufacturing facilities, smart factories leverage interconnected systems to make autonomous decisions and adapt quickly to changing conditions.
These facilities enhance operational efficiency by minimizing waste, optimizing resource allocation, and maintaining consistent quality standards. The integration of physical production systems with digital technologies creates a responsive manufacturing ecosystem that continuously improves through data-driven insights. This represents a fundamental shift from reactive to proactive production management.
Core Technologies Driving Smart Factories
Several cutting-edge technologies form the backbone of modern smart factory implementations:
- Internet of Things (IoT): Networks of sensors connect machinery and equipment to the internet, enabling constant communication and data collection throughout the production process. These sensors monitor everything from environmental conditions to equipment performance metrics.
- Artificial Intelligence (AI): Advanced algorithms analyze production data to identify patterns, predict maintenance needs, and optimize processes automatically. AI systems can make split-second decisions that would be impossible for human operators to manage at scale.
- Big Data Analytics: Sophisticated analysis of large datasets helps manufacturers identify inefficiencies, predict market trends, and make evidence-based strategic decisions. This transforms raw data into actionable intelligence.
- Robotics and Automation: Collaborative robots and automated systems handle repetitive, dangerous, or precision-requiring tasks with superior accuracy and consistency. These systems work alongside human operators to enhance overall productivity.
- Cybersecurity: Comprehensive protection measures safeguard interconnected systems from external threats and unauthorized access. As connectivity increases, robust security becomes increasingly essential.
Traditional Factories vs. Smart Factories: Key Differences
Traditional manufacturing facilities typically rely heavily on manual labor and oversight, with limited digital integration between different production stages. Information often exists in isolated silos, preventing seamless communication across departments and processes. Decision-making in traditional factories tends to be reactive rather than proactive.
In contrast, smart factories create a digitally unified environment where all elements communicate continuously. They respond rapidly to changes, adapt processes automatically, and produce higher-quality products with greater consistency. The following table illustrates the fundamental differences:
The Historical Evolution of Manufacturing
The journey toward modern smart factories follows a clear historical progression. Manufacturing began with artisanal production, where skilled craftspeople created products entirely by hand. The Industrial Revolution introduced mechanization, allowing for increased production volume through powered machinery.
The 20th century brought assembly lines and mass production techniques, dramatically increasing output while reducing costs. Later, computer numerical control (CNC) machines and programmable logic controllers (PLCs) introduced the first wave of automation and computerization to the factory floor.
Now, Industry 4.0 represents the convergence of physical and digital systems, with smart factories at its center. This evolution demonstrates how technological innovation continuously transforms manufacturing processes, with each advancement building upon previous developments to create more efficient, productive, and flexible production systems.
Essential Technologies in Smart Factories
Internet of Things (IoT): Creating Connected Manufacturing Environments
IoT technology forms the nervous system of a smart factory, connecting equipment, sensors, tools, and systems across the manufacturing environment. This comprehensive network enables seamless communication between previously isolated machines and processes. Real-time data transmission across this network facilitates better coordination, faster problem identification, and more responsive manufacturing operations.
In practice, IoT integration might include temperature sensors on production equipment, RFID tags on components moving through assembly, vibration sensors on motors, and connected quality control stations. These elements work together to create a continuous flow of operational data that supports decision-making at all levels. For example, a bearing showing unusual vibration patterns can trigger an alert before catastrophic failure occurs, allowing for planned maintenance rather than emergency repairs.
Artificial Intelligence and Machine Learning: Enhancing Decision-Making
AI and machine learning capabilities transform raw data from connected devices into meaningful insights and autonomous actions. These technologies enable smart factories to identify patterns that would be invisible to human observers, predict equipment failures before they occur, and optimize production parameters automatically.
Machine learning algorithms continuously improve their accuracy as they process more data, creating a system that becomes increasingly intelligent over time. For example, an AI system might analyze thousands of product images to detect subtle quality issues that would escape visual inspection. Similarly, machine learning can optimize energy consumption by identifying the perfect balance between production speed and power usage under varying conditions.
Robotics and Automation: Achieving Precision and Consistency
Robotic systems have evolved beyond simple repetitive tasks to become sophisticated collaborators in the manufacturing process. Modern industrial robots and cobots (collaborative robots) handle operations requiring extreme precision, consistency, or that present safety risks to human workers.
These systems work tirelessly in the smart factory environment, maintaining consistent production rates and quality levels regardless of shifts, breaks, or human fatigue factors. Advanced vision systems and tactile sensors allow robots to adapt to variations in components or positioning, while sophisticated programming enables complex decision-making during assembly operations.
For instance, automotive manufacturers use robotic welding systems that can adjust parameters in real-time based on material thickness variations, ensuring consistent weld quality across thousands of connection points.
Big Data Analytics: Transforming Information into Action
The volume of data generated within a smart factory is enormous, often reaching terabytes per day in large facilities. Big data analytics platforms transform this raw information into actionable intelligence that drives operational improvements and strategic decision-making.
These systems identify inefficiencies, predict maintenance requirements, and optimize production flows by analyzing historical and real-time data streams. Visual dashboards provide managers with clear insights into factory performance, while automated alerts highlight issues requiring attention.
For example, a pharmaceutical manufacturer might use big data analytics to identify subtle correlations between environmental conditions and product quality, allowing for proactive adjustments to maintain consistent results.
Cybersecurity: Protecting Critical Manufacturing Infrastructure
As smart factories become increasingly connected, robust cybersecurity measures become essential. Manufacturing facilities represent high-value targets for cyberattackers due to their economic importance and the potential for disruption.
Comprehensive security protocols protect intellectual property, prevent unauthorized system access, and ensure continuous operations. These measures include network segmentation, encrypted communications, access controls, continuous monitoring, and regular security audits.
The consequences of inadequate security can be severe, ranging from production downtime to safety incidents or intellectual property theft. Companies implementing smart factory solutions must treat cybersecurity as a fundamental requirement rather than an optional add-on.
Benefits of Implementing Smart Factory Solutions
Enhancing Operational Efficiency and Reducing Costs
Smart factory implementations deliver measurable improvements in operational efficiency across multiple dimensions. Real-time monitoring and analytics help identify and eliminate production bottlenecks, reducing cycle times and increasing throughput without additional capital investment.
Automated quality control systems catch defects earlier in the production process, reducing waste and rework costs significantly. Predictive maintenance capabilities minimize unplanned downtime by addressing potential equipment failures before they occur, improving overall equipment effectiveness (OEE).
These efficiency gains translate directly to cost savings. Labor productivity increases as workers focus on value-added tasks rather than routine monitoring or data collection. Material waste decreases through optimized processes and earlier defect detection. Energy consumption often drops by 10-20% through intelligent management of production equipment and facility systems.
For example, a consumer electronics manufacturer implemented smart factory technologies and reduced assembly costs by 15% while increasing production volume by 20%.
Improving Product Quality and Customization Capabilities
Quality improvements represent one of the most significant benefits of smart factory implementation. Continuous monitoring throughout the production process ensures consistent adherence to specifications, while automated inspection systems detect subtle defects that might escape visual inspection.
Digital process controls maintain optimal parameters for each operation, reducing variation and ensuring consistent results. When deviations occur, the system can automatically adjust parameters or alert operators before quality issues develop.
Perhaps most importantly, smart factories enable cost-effective mass customization. Flexible production systems can switch between product variants with minimal changeover time, allowing manufacturers to produce smaller batches economically. This capability helps companies respond to changing consumer preferences without sacrificing efficiency or quality.
A footwear manufacturer, for instance, implemented smart factory technologies to enable direct-to-consumer customization while maintaining production efficiency comparable to traditional mass production.
Enabling Real-Time Data-Driven Decision Making
Access to comprehensive real-time data transforms management capabilities within smart factory environments. Decision-makers can view current conditions across the entire facility, identifying issues as they develop rather than after they impact production.
Performance metrics become immediately available, allowing supervisors to address productivity or quality issues during the same shift rather than discovering them in next-day reports. Resource allocation decisions can be optimized based on actual conditions rather than estimates or historical patterns.
This real-time visibility extends beyond the factory floor to supply chain management, enabling better coordination with suppliers and distribution partners. For example, a food processing company uses smart factory data to adjust production schedules based on real-time sales information, reducing inventory costs while maintaining product freshness.
Promoting Sustainability through Resource Optimization
Smart factories contribute significantly to sustainability goals through optimized resource utilization. Energy management systems monitor consumption patterns and automatically adjust settings to minimize waste, particularly during non-production periods.
Predictive maintenance reduces the environmental impact of manufacturing by extending equipment lifespans and minimizing emergency repairs. Optimized production processes reduce material waste through precise control and early defect detection.
Many companies report 15-30% reductions in energy consumption after implementing comprehensive smart factory solutions. For example, a chemical processor reduced water usage by 25% and energy consumption by 18% through intelligent process controls and equipment monitoring systems.
Case Studies of Successful Smart Factory Implementations
Industry Leaders: Siemens and Bosch
Leading industrial companies have embraced smart factory principles with impressive results. Siemens has implemented digital twin technology at its Amberg electronics plant, creating virtual replicas of physical production systems for simulation and optimization. This approach has reduced defect rates to below 15 parts per million while increasing productivity by over 140%.
Bosch has deployed advanced IoT and automation solutions across multiple facilities, connecting over 120,000 machines worldwide. Their approach combines centralized data analysis with localized intelligence, enabling rapid response to changing conditions. At their Anderson, South Carolina plant, these technologies have increased productivity by 25% and reduced quality deviations by over 30%.
Improved Productivity and Cost Savings
Real-world implementations consistently demonstrate significant performance improvements. A pharmaceutical manufacturer achieved a 30% increase in overall equipment effectiveness (OEE) through predictive maintenance and process optimization technologies. An aerospace components supplier reduced labor costs by 22% while increasing output by 15% through strategic automation and digital work instructions.
A consumer packaged goods company implemented smart factory solutions across its production network, achieving $27 million in annual savings through reduced downtime and improved quality. Their predictive maintenance program alone reduced unplanned downtime by 68%, representing millions in avoided losses.
Quality Assurance and Customization Capabilities
Advanced sensor networks and machine vision systems have transformed quality control capabilities. An automotive parts manufacturer reduced defect rates by 87% after implementing AI-powered inspection systems across critical production lines. These systems identify subtle flaws that would be invisible to human inspectors, ensuring consistent quality.
The customization benefits of smart factory implementation are equally impressive. A furniture manufacturer implemented flexible automation systems that reduced changeover times between product variants from hours to minutes. This capability enabled them to offer custom configurations without price premiums, creating a significant competitive advantage.
Sustainability and Resource Management Achievements
Energy tracking and optimization systems have delivered substantial sustainability improvements across various industries. A food processing facility reduced energy consumption by 23% through intelligent monitoring and automated adjustments to production equipment. A textile manufacturer decreased water usage by 35% through precise process controls and real-time monitoring.
Predictive analytics have helped companies reduce their environmental footprint while improving operational performance. For example, a paper products manufacturer used advanced analytics to optimize fiber usage, reducing raw material consumption by 8% while maintaining product quality specifications.
Challenges and Risks in Transitioning to a Smart Factory
Managing High Initial Investment Costs
The financial requirements of smart factory implementation represent a significant challenge for many organizations. Equipment costs, software licensing, system integration, and facility modifications can require substantial capital investment. This initial outlay can be particularly challenging for small and medium-sized enterprises with limited financial resources.
Beyond the direct technology costs, companies must consider the expenses associated with employee training, process redesign, and potential production disruptions during implementation. These factors can extend the payback period for smart factory investments, requiring careful financial planning and phased implementation approaches.
Many companies address these challenges through staged deployment strategies, beginning with high-impact areas that deliver rapid returns on investment. Others explore partnership models with technology providers that reduce initial capital requirements through subscription-based services or performance-based contracts.
Addressing Cybersecurity Threats and Data Privacy Concerns
The increased connectivity of smart factory environments creates new security vulnerabilities that must be addressed. Manufacturing systems that were previously isolated now connect to enterprise networks and potentially to external partners, creating potential entry points for cyberattacks.
Data privacy concerns also emerge as production systems generate increasing volumes of potentially sensitive information. Companies must establish clear policies regarding data ownership, access controls, and retention practices to protect proprietary information while enabling beneficial data sharing.
Effective mitigation strategies include implementing defense-in-depth security architectures, conducting regular vulnerability assessments, and developing comprehensive incident response plans. Employee training on security best practices is equally important, as human factors often represent the weakest link in cybersecurity defenses.
Navigating Workforce Adaptation and Skill Gaps
The transition to smart factory operations often encounters resistance from existing workforce members who may feel threatened by automation or lack confidence in their ability to adapt to new technologies. This resistance can slow implementation and reduce the effectiveness of new systems.
Simultaneously, many organizations struggle to recruit employees with the specialized skills required to implement and maintain advanced manufacturing technologies. The competition for talent in areas such as industrial IoT, data science, and cybersecurity is intense, creating staffing challenges for manufacturing organizations.
Successful companies address these challenges through comprehensive training programs that help existing employees develop new skills. They also emphasize the ways technology enhances human capabilities rather than replacing workers, helping to alleviate fears and build support for digital transformation initiatives.
Overcoming Integration Complexity with Legacy Systems
Most manufacturers must integrate new smart factory technologies with existing equipment and systems, creating significant technical challenges. Legacy machines often lack native connectivity capabilities, requiring retrofitting with sensors and communication interfaces.
Existing enterprise systems—such as ERP, MES, and quality management platforms—may use proprietary data formats or communication protocols that complicate integration with new technologies. These compatibility issues can increase implementation costs and extend project timelines.
Companies address these challenges through careful planning and phased implementation approaches. They often begin by establishing a clear reference architecture for their digital manufacturing environment, then prioritize integration points based on business value. Edge computing solutions can help bridge the gap between legacy equipment and modern digital platforms.
Strategies for Successful Smart Factory Implementation
Overcoming Financial Barriers
Organizations can manage the financial challenges of smart factory implementation through several proven strategies. Starting with small, focused pilot projects allows companies to demonstrate value before committing to larger investments. These initial projects should target specific pain points with clear metrics for success.
Developing a clear business case that quantifies both tangible and intangible benefits helps secure executive support and funding. This analysis should include productivity improvements, quality gains, reduced maintenance costs, and enhanced customer satisfaction.
Many governments and industry associations offer grants, tax incentives, or subsidized financing for digital manufacturing initiatives. For example, the U.S. Manufacturing Extension Partnership provides technical assistance and funding for small and medium-sized manufacturers implementing advanced technologies.
Ensuring Robust Cybersecurity
Protecting smart factory systems requires a comprehensive security strategy that addresses both technical and human factors. Regular security assessments identify vulnerabilities before they can be exploited, while network segmentation limits the potential impact of any security breach.
Strong authentication protocols, including multi-factor authentication for critical systems, help prevent unauthorized access. Regular security updates and patch management ensure that known vulnerabilities are addressed promptly.
Employee security awareness training remains essential, as social engineering attacks often target personnel rather than technical vulnerabilities. Establishing clear security policies and procedures helps create a culture where security is everyone’s responsibility.
Workforce Development and Change Management
Successful smart factory implementations require both technical expertise and organizational change management. Companies should invest in comprehensive training programs that help employees develop the skills needed to work effectively with new technologies.
Cross-functional implementation teams that include representatives from operations, engineering, IT, and quality help ensure that multiple perspectives are considered during system design and deployment. These teams can also serve as champions for the new technologies within their departments.
Clear communication about how digital technologies will affect job roles and responsibilities helps address employee concerns and build support for transformation initiatives. Many successful implementations emphasize how technology enhances human capabilities rather than replacing workers.
The Future of Smart Factories: Trends and Predictions
Increasing Adoption of 5G and Edge Computing
The rollout of 5G networks promises to transform smart factory capabilities through dramatically increased bandwidth, reduced latency, and support for massive numbers of connected devices. These characteristics will enable new applications requiring real-time communication between multiple systems.
Edge computing—processing data closer to its source rather than sending everything to centralized systems—will become increasingly important in manufacturing environments. This approach reduces latency for time-critical applications while minimizing bandwidth requirements and enhancing resilience.
Together, these technologies will enable more sophisticated real-time applications such as augmented reality maintenance support, autonomous mobile robots, and highly responsive quality control systems. For example, a maintenance technician might use AR glasses connected via 5G to access real-time diagnostic information while repairing equipment.
Advancements in AI and Autonomous Systems
Artificial intelligence capabilities continue to advance rapidly, with manufacturing applications evolving from basic analytics to sophisticated autonomous decision-making. Future smart factories will feature AI systems capable of managing complex production environments with minimal human intervention.
Reinforcement learning techniques will allow manufacturing systems to optimize themselves continuously, identifying improvement opportunities that might escape even experienced human operators. These self-optimizing systems will adjust process parameters dynamically based on changing conditions and goals.
Autonomous robots will evolve beyond simple repetitive tasks to handle complex, variable operations previously requiring human judgment. These advanced systems will work collaboratively with human operators, each focusing on their respective strengths.
Integration of Digital Twins for Simulation and Optimization
Digital twin technology—creating virtual replicas of physical assets and processes—will become a standard element of smart factory implementations. These detailed digital models enable simulation-based optimization without disrupting actual production operations.
Engineers will use digital twins to test process changes virtually before implementing them physically, reducing risk and accelerating innovation. Operators will receive predictive guidance based on simulations that consider current conditions and historical performance data.
The fidelity of these digital models will continue to improve as sensor technology advances and simulation techniques become more sophisticated. Eventually, many factories will operate continuous simulations that run slightly ahead of actual production, providing preemptive guidance to operators and systems.
The Evolution Toward Fully Autonomous Smart Factories
The long-term vision for many manufacturers involves developing facilities that can operate with minimal human intervention. These fully autonomous smart factories would manage routine operations independently, calling for human assistance only when facing unusual situations.
While complete autonomy remains a distant goal for most applications, incremental progress continues across multiple fronts. Automated material handling systems, self-optimizing production lines, and intelligent quality control systems represent steps toward this vision.
The economic and quality benefits of autonomous operation will drive continued investment in these capabilities, particularly in industries facing labor shortages or extreme quality requirements. However, human judgment and creativity will remain essential for innovation and handling exceptional situations.
Impact of Global Supply Chain Dynamics on Smart Factory Design
Recent supply chain disruptions have highlighted the need for manufacturing agility and resilience. Future smart factory designs will increasingly emphasize flexibility and adaptability to changing supply conditions and market requirements.
Localized production capabilities will become more important as companies seek to reduce supply chain risks through regional manufacturing strategies. These facilities will require highly flexible production systems capable of handling diverse product ranges efficiently.
Advanced analytics and AI will help manufacturers anticipate disruptions and adjust production plans accordingly. Digital supply chain integration will provide real-time visibility into material availability and logistics constraints, enabling more responsive production scheduling.
Expert Insights and Industry Forecasts
Leading manufacturing technology experts project accelerating adoption of AI and automation technologies over the next decade. According to industry analysts, approximately 70% of manufacturers are currently implementing or planning smart factory initiatives as central elements of their competitive strategy.
Market forecasts suggest the global smart factory market will expand at a compound annual growth rate of approximately 11% through 2030, reaching a value exceeding $400 billion. This growth reflects both the proliferation of enabling technologies and the demonstrated business value of digital manufacturing approaches.
Actionable Tips for Staying Ahead in Smart Manufacturing
To position your organization for success in the evolving manufacturing landscape:
- Invest in ongoing staff training programs focused on digital skills and systems thinking. Human capabilities remain essential even as automation increases.
- Build flexible, scalable technology architectures that can adapt to changing requirements and incorporate new capabilities as they emerge.
- Participate actively in industry consortia and standards organizations to stay informed about emerging technologies and best practices.
- Develop clear metrics for measuring smart factory performance that align with strategic business objectives rather than focusing solely on technology implementation.
- Create a culture that embraces continuous improvement and sees technology as an enabler rather than a threat.
Conclusion: Embracing the Smart Factory Revolution
Smart factories are fundamentally transforming manufacturing by combining advanced digital technologies with traditional production expertise. They blend connectivity, automation, and intelligence to create manufacturing environments that produce better products faster and more efficiently.
Success in this new manufacturing paradigm requires thoughtful planning, investment in both technology and people, and a willingness to embrace continuous innovation. Forward-thinking companies recognize that digital transformation is not a one-time project but an ongoing journey of improvement and adaptation.
As we look toward the future, tomorrow’s factories will be increasingly intelligent, efficient, and sustainable. Organizations that embrace these capabilities today position themselves for competitive advantage in an increasingly dynamic global marketplace. The time to begin your smart factory journey is now—whether through small pilot projects or comprehensive transformation initiatives.
By leveraging the principles and technologies outlined in this guide, manufacturers of all sizes can unlock new levels of productivity, quality, and agility. The smart factory revolution is underway, offering unprecedented opportunities for those ready to embrace the future of manufacturing.
Additional Resources:
About the author
Recent articles
Quad Core Dedicated Servers
Interested in Quad Core Dedicated Servers? View our inventory. What is a quad core dedicated...
Read More8 Core Dedicated Servers
For website owners looking to eliminate their hardware bottlenecks, the massive power capabilities of an...
Read MoreHow Unmetered Servers Can Help Businesses Grow
If you have a business website that is growing and expanding, it is essential that...
Read More